PROJECT OVERVIEW.
Freeboring in Sandstone
All of the bores were in sandstone which allowed the use of slip lining the carrier pipe into a Freebore. Here, an oversized bore (slightly larger than the collar of the pipe) was bored, the drilling rods retracted then the GRP carrier main inserted into the bore on skids. The annulus was then grouted and the pipe floats into its final set position at the top of the bore – held down with spacers.
For this Project, a DN 300 GRP SN20,000 collared pipe was inserted into a 440mm diameter bore. As no temporary casing or sleeve was required, a significant financial saving was achieved. This is a major advantage of the Pezzimenti-designed Freebore method.
The first 5 bores went as planned including the bore under Canterbury Road. During the final bore towards the upstream manhole, an obstruction was incurred – 8 metres below Charles Street.
Encountering Rock Anchors
The head was retracted (another major advantage of Freeboring) and a CCTV inspection of the bore was carried out. The obstruction was a high tensile rock anchor from an adjacent building basement. Investigations showed that this rock anchor was a temporary support. To overcome this obstacle, Pezzimenti replaced the bore cutters with a specially designed cutting attachment.
The cut was made at exactly 440mm and approx 200mm deep into the bore then retracted. Just enough to cut the cable. The head was then retracted and the original cutters were fitted again. The steel cable broke up and came back into the vacuum. Boring continued for another 3m then another rock anchor was hit. This process continued for 5 rock other anchors – all 3 metres apart.
Freeboring Crucial to the Success of this Project
This final bore was to be a connection into an old manhole, 8 metres deep on a road without disruption to traffic.
The manhole was reached and the cutters bored up to the reo into the base. From there, the head was again retracted and replaced with a deep core section. The corer cut approximately 600mm into the wall, base and benching where it was broken off in the manhole. The “core” came back with the corer and the connection went ahead as planned.
In this instance, the Freebore method was crucial to the success of the project. Despite all potential risks being assessed after the inspection of the Geotechnical Report, a man-made obstacle was still encountered – a rock anchor in this case.
Without the flexibility to retract the drill head through the bore and change strategy after hitting the obstruction, the bore would not have been possible. Worst still, if the bore was pipejacked, as is usually required with alternative microtunnelling equipment, the head would have been stuck and required to be drilled down on to rescue it.
In this case, eight metres deep on a busy inner-Sydney street!
MICROTUNNEL 1.
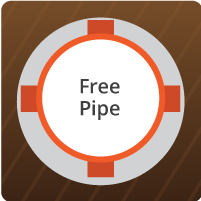
Free Pipe by Freebore Method
Length. 27.5m
Diameter. 440
Ground. Sandstone
Casing Pipe. None
Carrier Pipe. 300GRP
MICROTUNNEL 2.
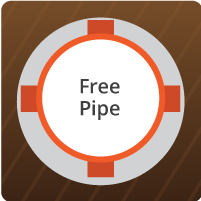
Free Pipe by Freebore Method
Length. 176m
Diameter. 440
Ground. Sandstone
Casing Pipe. None
Carrier Pipe. 300GRP
MICROTUNNEL 3.
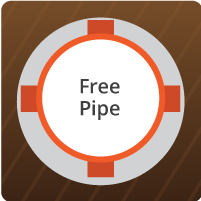
Free Pipe by Freebore Method
Length. 36.5m
Diameter. 440
Ground. Sandstone
Casing Pipe. None
Carrier Pipe. 300GRP
MICROTUNNEL 4.
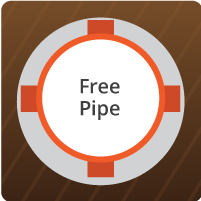
Free Pipe by Freebore Method
Length. 82m
Diameter. 440
Ground. Sandstone
Casing Pipe. None
Carrier Pipe. 300GRP
MICROTUNNEL 5.
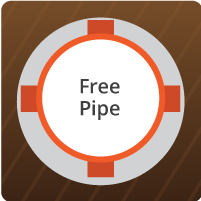
Free Pipe by Freebore Method
Length. 74m
Diameter. 440
Ground. Sandstone
Casing Pipe. None
Carrier Pipe. 300GRP
MICROTUNNEL 6.
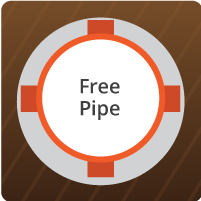
Free Pipe by Freebore Method
Length. 64m
Diameter. 440
Ground. Sandstone
Casing Pipe. None
Carrier Pipe. 300GRP