PROJECT OVERVIEW.
Freeboring Project
Pezzimenti was able to offer a Freebore solution whereby the bore was completed and pipe installed post bore. Freeboring eliminated the need for access shafts to remove the heads at the end of the drives.
Ground Condition
The ground condition was self-supporting shale and siltstone. A high torque head was designed for this rock over the given distance. The smaller bore was completed using our vacuum spoil removal system. The larger bore was undertaken with our larger gear which uses an auger spoil removal system.
Launching Microtunnelling Head
During Operation
Deep Shaft
The Bucket Elevator which transports the soil from the shaft to the dump truck
DN600 x 109m:
Cherrybrook station was constructed by cut and cover. The first bore housed a DN600 Reinforced Concrete Jacking Pipe which drained station box and surrounding rail track. From a launch shaft 109m from the edge of the station box wall, an 800mm diameter microtunnel was freebored to a proposed pit location just inside the station box. The head and drill rods were removed and the DN600 pipes sliplined into the bore. This was carried out without disturbing the critical construction occurring within the station box. The connection from the station box drainage to the already installed microtunnel was done later when it best suited the main project.
The Freebore method also saved valuable time and space for the construction of the receive pit in the main station.
Microtunnel Details
The first stage of the Cherrybrook Station works was the excavation of the station box which acted as the tunnel portal for the TBM drives. Temporary rock anchors had been used to support the concrete pile walls for the bulk excavation of the station box. Some of the rock anchors were installed along the alignment of the stormwater microtunnels and were to be removed by the client prior to boring. However, at approx 93m in, a hard object was struck and a rod near the head broke. The Freeboring method allowed us to remove the head from the microtunnel to replace the drilling rod. A CCTV was put up the bore which showed the remnants of a rock anchor in the top left hand corner of the face. The client elected to dig up the bore at that location to remove the rock anchor. The bore then continued through to the proposed pit
Cherrybrook Station Development
Operator Paul utilises CCTV Camera and CCTV monitor to oversee microtunnelling
View down Freebore with laser visible
Rock Anchors were encountered along the bore these pieces coming back in the spoil.
Rock Anchor in the path of microtunnel. The Freeboring method enabled Pezzimenti to pull back the head so the anchors could be removed
DN1650 x 129m:
The second bore was 1650 diameter to house a DN1350 Reinforced Concrete Jacking Pipe. This bore proved more troublesome than the first.
Microtunnelling progressed in Freeboring mode until another rock anchor was hit at the approximate location as was encountered on the DN600 microtunnel. The larger cutters actually tore through the rock anchor but not without damage to the rods and drive system. The Ø1650 head was withdrawn, repairs made and sent back to the face to continue drilling.
Microtunnel Details
Digging up the rock anchors at this location was not an option, so the client removed the rock anchors by vertical drilling with a high torque specialised vertical boring rig. The void was backfilled with sand and cement mix and microtunnelling continued. More rock anchors were encountered under the base slab of the box station and were removed by coring to allow microtunnelling to continue.
The bore was completed on target and the 1350 concrete stormwater pipes inserted through the microtunnel to a circular shaft for connection to the suburban stormwater system.
MICROTUNNEL 1.
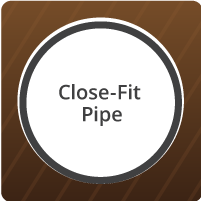
Close Fit Pipe by Freebore Method
Length. 109m
Diameter. 800
Ground. Shale/Siltstone
Casing Pipe. N/A
Carrier Pipe. 600 RC RRJ JP
MICROTUNNEL 2.
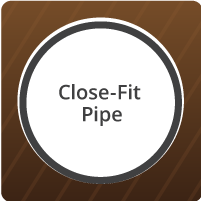
Close Fit Pipe by Freebore Method
Length. 129m
Diameter. 1650
Ground. Shale
Casing Pipe. N/A
Carrier Pipe. 1350 RC RRJ JP