PROJECT OVERVIEW.
Self-Supporting Ground
The majority of the pipeline was located in shale. This meant that steel sleeve was not required as an enveloper pipe – given the ground self supports – the bore stays true to shape until grouted. The original design had steel sleeve along the entire route – by not using steel sleeve this saved the developer and SWC approx $200/m and also saved time by not having to insert it.
Where the ground didn’t self support or where the bore travelled under an existing dam, sleeve was required.
All of the bore shafts were located in quite difficult to get to areas. Machinery configuration had to be flexible to accommodate some tight situations. The vacuum could stand remote from the shaft using vacuum hose to join in with the jacking frame.
Weather Conditions Overcome
During March and April, access to parts of the golf course were limited due to flooding so the project had to stop for two months. Heavy vehicles simply couldn’t get to the areas required.
Once the weather dried up again, the works were completed with time being caught by up using two crews – one to bore and the other to follow pushing in the pipes and grouting. This saved around 4 days per bore.
1049m was microtunnelled on this project.
Site Layout next to putting green and fairway
Site Setup
Site Setup
The trailer mounted Hydraulic powerpack and the Vacuum truck were main equipment on site. The top man prepares a drill rod for cranage by excavator
Drill rods ready for loading via the container truck
Top man lowering rods down into shaft using the gantry winch
Loading the 406 Steel Casing
Pipejacking the 406 Steel Casing
The vacuum truck captures and transports spoil
The Hydraulic power pack and vacuum truck setup
300 uPVC stockpile with spacers attached
MICROTUNNEL 1.
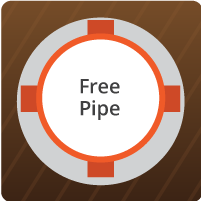
Free Pipe by Freebore Method
Length. 86m
Diameter. 630
Ground. Shale
Casing Pipe. N/A
Carrier Pipe. 375GRP
MICROTUNNEL 2.
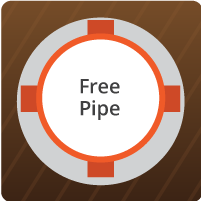
Free Pipe by Freebore Method
Length. 143m
Diameter. 630
Ground. Shale
Casing Pipe. None
Carrier Pipe. 375GRP
MICROTUNNEL 3.
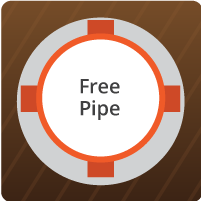
Free Pipe by Freebore Method
Length. 77m
Diameter. 630
Ground. Shale
Casing Pipe. None
Carrier Pipe. 375GRP
MICROTUNNEL 4.

Pipe in a Pipe by Pipejack Method
Length. 61m
Diameter. 530
Ground. Shale
Casing Pipe. 508 Steel
Carrier Pipe. 300 uPVC
MICROTUNNEL 5.

Pipe in a Pipe by Pipejack Method
Length. 100m
Diameter. 530
Ground. Shale / Clay
Casing Pipe. 508 Steel
Carrier Pipe. 300 uPVC
MICROTUNNEL 6.

Pipe in a Pipe by Pipejack Method
Length. 103m
Diameter. 530
Ground. Shale / Clay
Casing Pipe. 508 Steel
Carrier Pipe. 300uPVC
MICROTUNNEL 7.

Pipe in a Pipe by Freebore Method
Length. 55m
Diameter. 530
Ground. Clay
Casing Pipe. 508 Steel
Carrier Pipe. 300 uPVC
MICROTUNNEL 8.
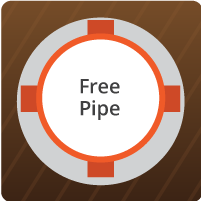
Free Pipe by Freebore Method
Length. 156m
Diameter. 440
Ground. Shale
Casing Pipe. None
Carrier Pipe. 300 uPVC
MICROTUNNEL 9.

Pipe in a Pipe by Pipejack Method
Length. 117m
Diameter. 430
Ground. Clay
Casing Pipe. 406 Steel
Carrier Pipe. 225 uPVC
MICROTUNNEL 10.

Pipe in a Pipe by Pipejack Method
Length. 90m
Diameter. 430
Ground. Clay
Casing Pipe. 406 Steel
Carrier Pipe. 225 uPVC
MICROTUNNEL 11.

Pipe in a Pipe by Pipejack Method
Length. 61m
Diameter. 430
Ground. Clay
Casing Pipe. 406 Steel
Carrier Pipe. 225 uPVC